Plasma Applied Ceramic Coatings In Fireboxes And Furnaces
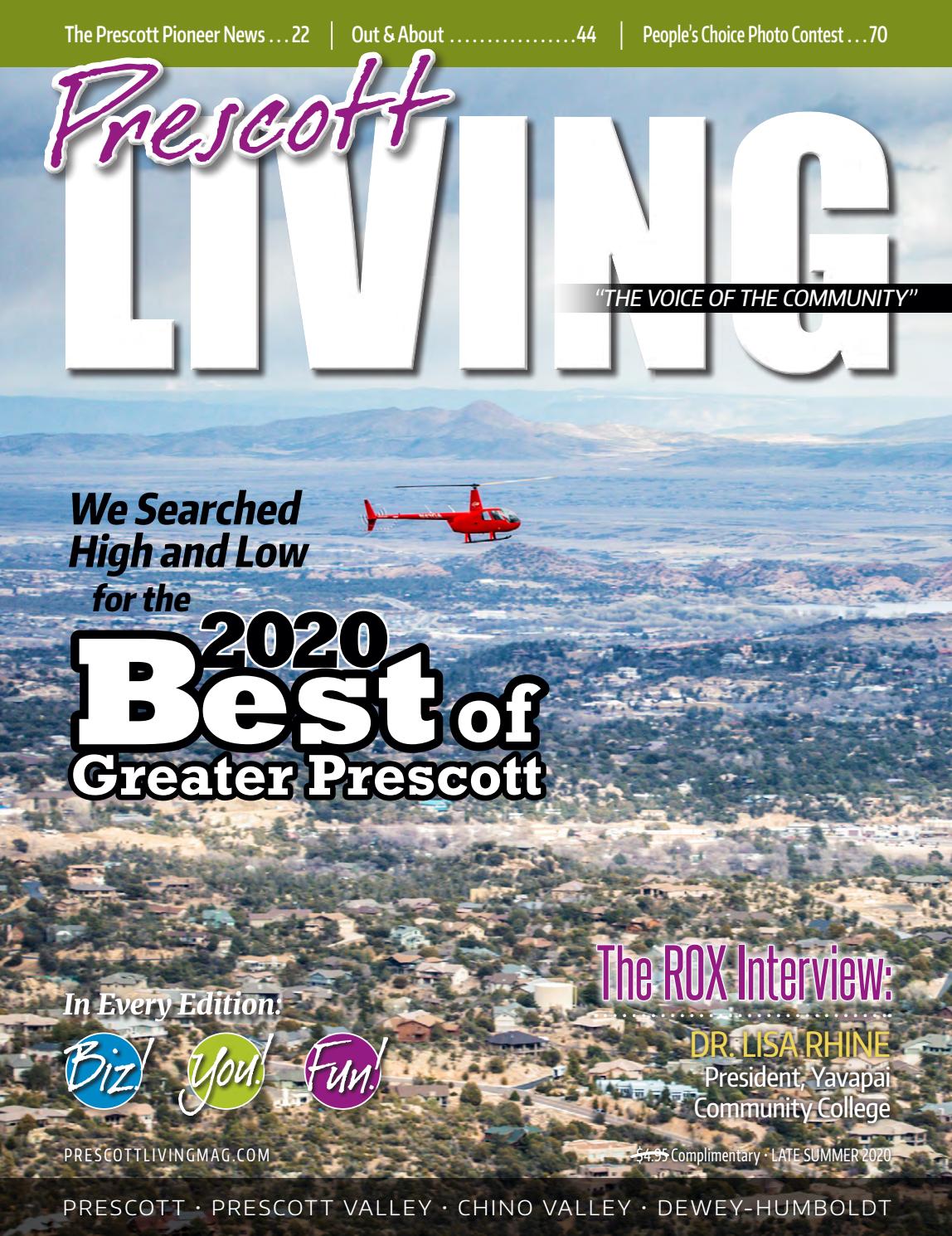
They have the advantage ofallowing the direct use offine feed materials.
Plasma applied ceramic coatings in fireboxes and furnaces. Asb industries plasma spray coating processes utilize heat energy to reach the melting point of the chosen ceramic chemistry. Degrees and withdrawn and cooled outside the crucible in the inert atmosphere of the induction furnace. Coating by opening during heating period and hence the. The zirconia thermal plasma coating is sprayed on to the metal parts at 500 1000 degrees f.
Steel aluminum leading provider of high performance coverings for coating applicators to bridle rollers for over 50 years. The major fields of the application of gas turbines. Ceramic top coats of plasma sprayed thermal barrier coatings. Thermal barrier plasma applied ceramic coatings our thermohold based plasma applied ceramic coatings have been developed to significantly reduce heat transfer providing lightweight and easily packaged coatings to reduce heat loss from hot components.
Plasma furnaces have been successfully applied to the production ofa variety ofmaterials particularly ferro alloys. Refractory coatings were applied to niobium substrates by vacuum plasma spray coating method. Wear resistant coatings and coverings extend life and reduce defects from the paper making process to finished products. A spray coating technique is an excellent method for surface metallization and ceramic deposition to widen the application fields of irreplaceable engineering polymers.
Materials processes and properties. Thermal barrier coatings tbcs are protective coatings applied to the surface of hot metallic sections in gas turbine engines. Protect your parts from residue build up and hot spots and short element life. The pressurized gas then speeds molten ceramic particles toward the substrate where they bond onto its surface.
Furthermore because the power input is not limited by the. The plasma gas flows around the cathode and then through the copper anode. As a result you will see a strongly adhering and high density coating. Since this system is very effective in heating and melting sprayed powder high quality ceramic coatings can be easily produced even at a small power using argon as the working gas.
Developments in plasma furnace technology by r t. Performance white delivers the ultimate in thermal barrier performance. At 30 kw or more the vickers hardness of the various ceramic coatings is 30 greater than that produced with a conventional type plasma spraying apparatus. Plasma coatings are applied using spray guns that feature water cooled copper anodes and tungsten cathodes.
Coatings plating s applies zirconia ceramic coating to resistance wire heating elements sic and mosi2 heating elements used in high temperature furnaces.